FAQs
-
What type of insulators does the E-Pro 8000 HVIC and E-Pro RG 1221 Grease protect?
Both the E-Pro 8000 HVIC and the E-Pro RG 1221 adheres strongly to Porcelain, Glass and Polymer / Composite Insulators. They will both enhance the hydrophobicity and prevent leakage current.
-
What is the difference between E-Pro 8000 HVIC and E-Pro RG 1221 Grease?
E-Pro 8000 HVIC is a Room Temperature Vulcanising silicone elastomer that readily cures and adheres as a hard rubber coating on the
insulator surface. E-Pro 8000 provides a highly hydrophobic surface for its entire life, and is not affected by UV light, chemical
contaminates, salt, sand, fly ash, cement dust, iron ore, extreme temperatures and corrosive environments.
E-Pro RG 1221 Grease is a high voltage insulator non curing compound. Its grease formulation gives insulators a long term resistance
to UV rays, chemical contaminates, salt, sand, fly ash, cement dust, iron ore, extreme temperatures, and corrosive environments. When
this high voltage insulator compound becomes covered with contaminants, it absorbs the pollutants as the fall on the insulators, enabling
the surface to be free of conductive materials that cause leakage current.
E-Pro 8000 HVIC has a longer service life because it does not absorb and bury the pollutants leaving the surface intact for a minimum of
eight to ten years and longer depending upon its service conditions.
E-Pro RG 1221 needs to be removed and replaced when excessive contamination becomes evident depending upon its service conditions.
-
How does E-Pro 8000 HVIC protect the insulator against leakage current and flashovers?
When the E-Pro 8000 compound is applied and cured, the hydrophobic factors (non conductive free fluid) controls the degree of wetting
of the surface contaminants. This free fluid rises to the surface of the RTV coating to form in droplets which prevents the surface
contamination from becoming wet and providing a conductive path that leads to leakage, arcing and possible flashovers. The free
fluids on the coating surface encapsulate the contaminants thus rendering them non conductive. The current cannot follow a conductive path down the insulator thus controlling and stopping leakage current leading to potential flashovers.
-
What type of contaminants does E-Pro protect against?
E-Pro protects against chemical contaminants, salt, sand, dirt, fly ash, cement dust, Iron ore and graphite dust. Certain types of
highly conductive industrial contaminants will require special needs and these are investigated on a case by case basis.
-
How is E-Pro 8000 applied to all types of Insulators?
Two ways the RTV coating can be applied: spray coating (most widely applied method) and paint brush / sponge glove by hand.
Before application, the insulator must be free and clean of dust, dirt, waxes, or grease. The surface should be cleaned with a denatured
solvent. If the insulators are coated with silicone grease, the grease must be completely removed by hand with denatured alcohol or by
fine grito cobb / soft pulverized limestone powder blasting method*. This preferred method will ensure complete grease removal and all of its contaminants. Diluting the E-Pro 8000 may be necessary for desirable spray application depending upon type of spray equipment
and current weather conditions. Use a high flashpoint solvent such as E Solv 207 for diluting purposes. A compressed air assisted airless
spraying unit with a minimum 25 to 1 ratio. Two to three coats of E-Pro 8000 HVIC with a 15 to 20 mm DFT minimum. The spray gun
should have a 1.8mm diameter nozzle to avoid thinning of the RTC coating. Approximately 20 to 30 minutes is required between coats
resulting in good adhesion to itself.
* E-Pro highly recommends the Corn Cobb / Limestone Powder Blasting Method and the Spray Coating Application by applied by
professionals such as Energized Substation Maintenance Inc. ESM Inc. can both clean and coat an Insulator "DE-ENERGIZED"
but Specializes in "ENERGIZED" Applications. www.ESM2000.com / ESM1@aol.com
-
Can E-Pro 8000 be applied "ENERGIZED".
Yes, it can be applied Energized by professionals such as Energized Substation Maintenance Inc. By applying the E-Pro 8000 while "Energized", it allows you to keep your plant operating without power shut down. When the E-Pro 8000 is applied while "De-Energized",
the system can be "Energized" immediately after coating is complete. Full cure of the coating will take approximately 8 hours depending
upon weather conditions.
-
How long will a single coat of E-Pro 8000 protect and should it be removed after its service life?
There are many factors for determining the life expectancy of E-Pro 8000. The insulator type, design, type of contaminant, and rate of
fall out on the surface of the insulator. From previous experience, a single application should provide protection for 8 to 10 years.
The original application coating will never have to be removed. Signs of wear (thinning) or a loss of hydrophobicity, providing the original
coating displays good adherence to the insulator, a proper cleaning (removing surface contaminants) and a recoating of the insulator
is recommended.
-
What happens to E-Pro 800 if it is applied to a contaminated surface?
The adhesion of the coating will be poor, thus shortening the intended life of this product. Putting E-Pro 8000 over a chemical
contaminants or a conductive surface could lead to interfacial tracking and eventual leakage.
-
What is the typical maintenance required to E-Pro 8000 during its service life?
E-Pro 8000 was designed to be virtually maintenance free. The coating surface can retain some contaminants and discoloration, but
is fully able to repel moisture as its intended to. Visual inspection is sufficient enough and / or a hydrophobicity test (water spray)
to determine if the coating needs to be cleaned.
-
How does E-Pro 8000 withstand dirt / sand blown particles?
E-Pro 8000 is strong rubber coating able to absorb the energy of dirt, sand, and small rock particles of a typical sandstorm. The surface
will show possible roughness and / or discoloration, but will not penetrate the coating to the bare insulator.
-
What is the typical shelf life of E-Pro 8000?
E-Pro 8000 has an expiration date on every 1 gallon / 5 gallon pale. It is 12 months from the date of manufacture and labeled accordingly.
-
What is the cost comparison of E-Pro 8000 to E-Pro RG 1221 grease?
E-Pro RG 1221 grease is substantially less kg for kg than E-Pro 8000 HVIC. However, the volume of E-Pro 8000 required per sq meter
of insulator surface is approximately 25% of the volume of E-Pro SG 1221 Grease needed for the same area. Even with the application
cost being about 20 to 25 percent more for E-Pro 8000, the savings would be realized at the time when the grease coating would be
removed and replaced. Labor and time savings to remove and replace the grease would contribute to the E-Pro 8000 savings.
-
Are E-Pro COATINGS AVAILABLE OUTSIDE OF THE UNITED STATES.
Yes, the experts at E-Pro can offer you a turnkey solution to your needs for insulator coating in the United States as well as globally.
|
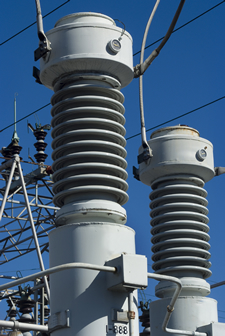
|